Carving wood with power/electrical tools is a great way to create delicate designs and carve intricate details that would be difficult using traditional tools, like chisels, knives, and gouges. Wood carving with power involves using motorized equipment that rotates a shaft with a cutting bur mounted on the end.
Power Wood Carving Pros and Cons
Power carving offers several advantages over wood carving with hand tools. However, power carving also comes with its drawbacks. Below are the benefits and drawbacks of power carving.
Benefits of Power Carving
- Removes wood quickly with precision. This is especially helpful when carving hardwoods.
- You can minimize splintering and fracturing when carving wood.
- You have better control when carving fine details than knives and gouges.
- You can also carve or grind metal and epoxies.
- Sanding is controlled and quicker.
- There is no need for sharpening tools.
- Woodcarvers who have difficulty with edge tools due to arthritis have an alternative in power carving.
Drawbacks of Power Carving
- The initial cost to buy power carving tools is high.
- Has different safety concerns, unlike traditional wood carving.
- It generates a lot of dust, which can harm some people.
Safety for Power Carvers
Safety should be among your top priorities for beginners looking to start power carving. For power carving, the primary safety considerations are dust inhalation and fire hazard from improper dust collection and disposal.
Dust
Inhaling dust is the biggest risk that a power wood carver faces. Grinding, cutting, and sanding all release dust. When inhaled, these small wood particles can cause allergic and respiratory problems. More serious risks are associated with inhaling the dust of exotic hardwoods.
A proper dust collection system can be used to minimize the risks of dust. The dust collection system works like a vacuum, pulling air and dust particles and trapping them in a filter. Dust collection systems come in different sizes and price ranges. There are portable ones, while some are incorporated into your woodworking workstation.
I recommend the SHOP FOX W1727 1 HP Dust Collector for woodcarvers who have small shops.
It is small in size and should work out of a small shop. For wood carvers, this will help minimize dust when power carving. It is also easy to put together; you should get it up and work easily.
However, you should know that no dust control system will trap all the dust particles. This is why a face mask should be used in addition to a dust collection system. Choose a good-fitting and comfortable mask that seals properly.
Body Protection
Besides dust, body safety equipment when dealing with power tools is welcome. Safety glasses or goggles protect our eyes from flying debris, metal particles, or materials from the burs. Glass lenses are better than plastic lenses because glass does not have much static electricity to hold dust. Some wood carvers will also prefer a full face shield when power carving.
Besides eye and face protection, greater potential for injury occurs when large carbide or steel burs accidentally slip or jump.
Large carbide or steel burs can inflict major damage and should be handled properly when power carving wood. Carving in the grain direction is the safest way to minimize potential accidents. Also, clamp down your project when using large and aggressive bits. You should also avoid loose clothing and tie back long hair to avoid it getting caught up in action.
The use of wood carving gloves is not recommended when power carving because if the glove fibers bet caught up, it can be dangerous. However, most new micro motor power carving equipment has breakers and fuses that will stop the machine in its tracks in such cases.
Power Carving Tools
Before you begin carving with power, you need a basic understanding of the tools used. Flexible shaft machines and micromotors are mainly used in power carving. Flexible shaft machines have greater torque but less speed. Let’s get into the details of these two below.
Flexible Shaft Machines
Flexible shaft machines are the major tool for power carving. Most power carvers will use a flexible shaft machine, from roughing out carvings to doing the detail work. This is the first power carving machine most beginners start buying. Unless you are power carving small or miniature carvings, I recommend you start with a flexible shaft machine.

VEVOR S-R Hanging Flex Shaft Grinder 230W Rotary Tool
A flexible shaft machine is comprised of a flexible shaft, a handpiece, and a foot pedal. The flexible shaft has a drive motor attached to 36 inches or a long flexible shaft. The handpiece is the part you hold and is attached to the shaft, while the foot pedal controls the rotational speed of the bur. The higher the shaft turns, the faster the bur will remove wood. The speed is measured in revolutions per minute (rpm).

The Handpiece of a Flexible Shaft Machine
The handpieces can vary in different sizes and shapes. Most of the handpieces from different manufacturers are interchangeable. The handpiece connects to the flexible shaft on one end and holds the bur or bit in a collet on the other end. With most handpieces, you can interchange the bits by changing the collet. Bigger bits/burs are great for roughing out, while smaller ones are good for shaping and detailing.

A Wood Power Carving of an Eagle in Flight
Micro Motors Machines
One of the major advantages of micromotor machines over flexible shaft machines is the speed. Micromotor machines can achieve speeds up to 50,000 rpm. The power is delivered via a control box that includes an off/off switch, a speed controller, and a floor control/manual switch. Although digital speed controllers are great for consistency, their cost is very high and not worth it.
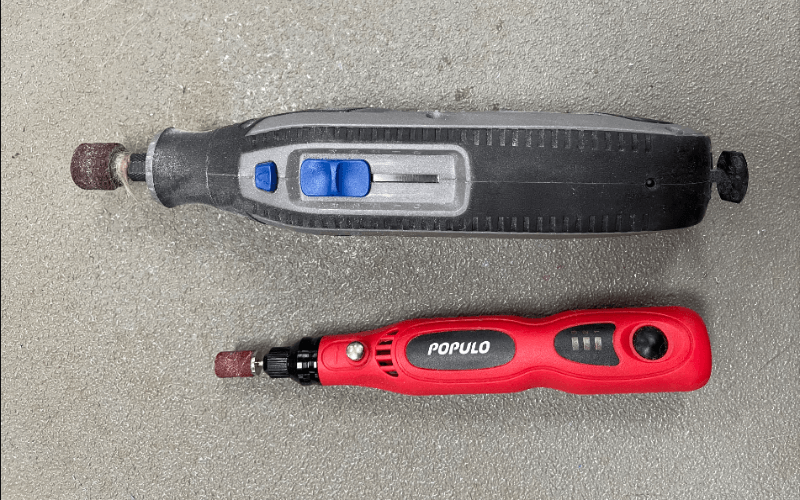
These are Two Cordless Rotary Tools Portable
Micromotors do not have a high torque in comparison to flexible shaft machines. In this case, they are not good for roughing out large carvings. Micro motors are good for detail carving and texturing. For most bird carvers, a micromotor machine is used for the highly detailed texture characteristics associated with that carving style. High speeds of micromotor machines also result in cleaner cuts.

Different types of wood power carving bits/burs
Other Power Carving Tools
The flexible shaft and micro motor machines are the most common tools used by power woodcarvers. However, other rotary tools are used by wood carvers for specific needs.
Air Turbine Machines
Wood carvers purchase air turbine machines with specific needs. They are great for removing a small amount of material faster and with greater precision. In addition to carving wood, air turbine machines are used to carve glass, egg shells, ceramic, metals, bone, and antler. Air turbine machines require an air compressor and can operate up to 400,000 rpm.
Angle Grinders
The use of an angle grinder in wood carving removes a large quantity of wood quickly and efficiently using a large carbide disc or toothed chain. Because using an angle grinder uses two hands, the wood being carved should be clamped securely. Wear safety glasses, a dust mask, and other protective clothing when using an angle grinder.

Use an Angle Grinder for Wood Carving
Chainsaw woodcarvers will also use an angle grinder to detail their carvings.
Apart from these power tools, reciprocating carvers and die grinders are also used in wood power carving. Woodburners are also employed to augment the detail and texturing made with a power carving machine before painting. Bird carvers use wood burners to create lifelike feathers.
Basics of Power Carving
- Wasting – Wasting is also called hogging. It refers to the removal of unwanted stock.
- Roughing – This refers to bringing a carving to a recognizable stage. A rough shape does not have detail, texture, or refinement.
- Relieving – This is raising a surface or shape away from the background. For example, a curl is relieved from the hair mass or ears from the sides of the head.
- Shaping – This process gives a refined carving to a general or roughed shape. The carving becomes recognizable at this point.
- Detailing – This gives finished detail to a refined shape. For example, the detailed shape of a head has details required by the refined shapes. The mouth has lips, the nose has nostrils, while any hair mass is more defined with separations, curls, etc.
- Texturing – This is the final stage and finishing refinement that will give character and reality to a carving. For example, wrinkles and creases on the head represent aging or age.
